Schneider Electric Smart Factory Boosts Product Quality Using AI-Based Automated Inspection
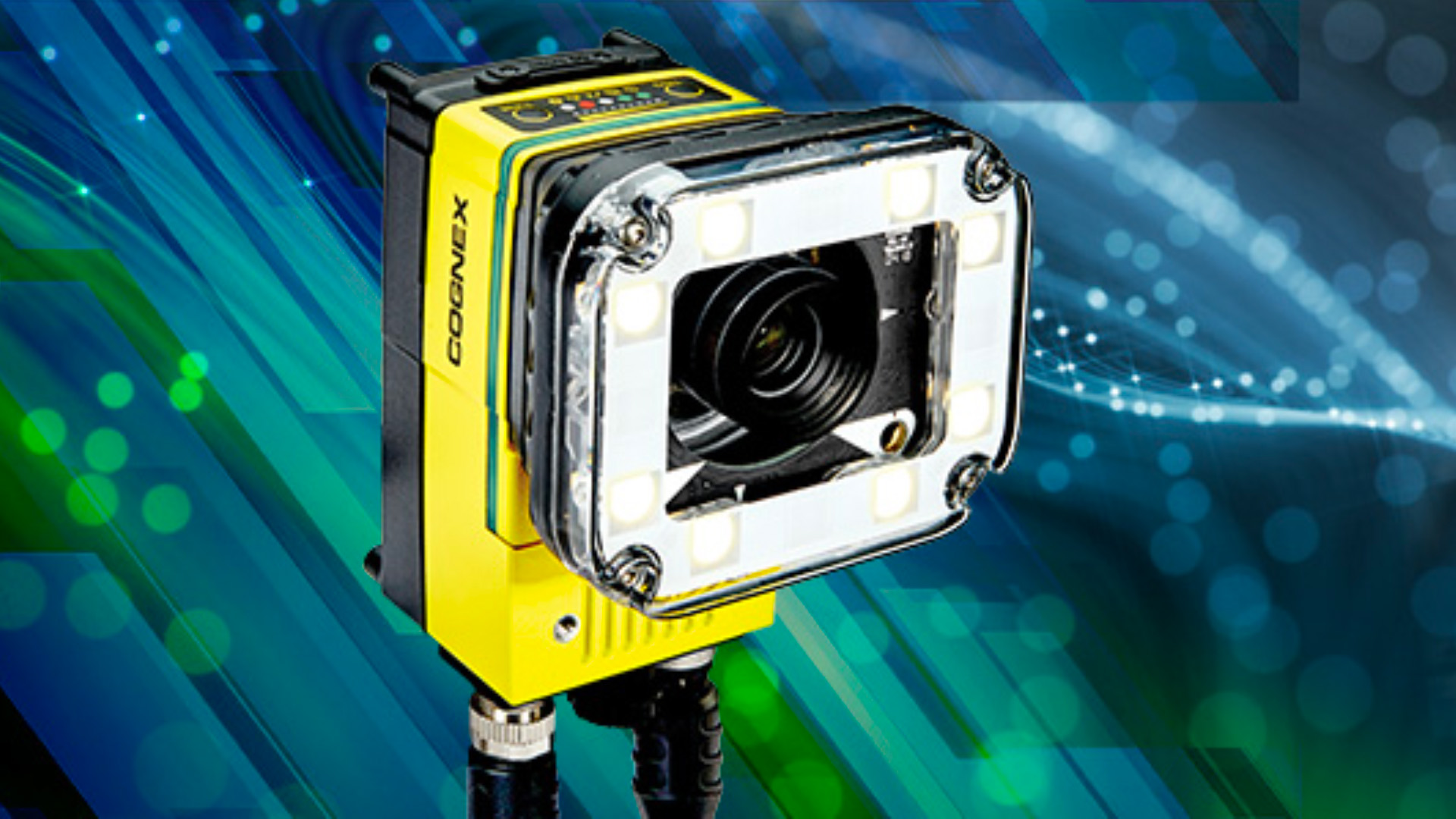
The ongoing miniaturization of electronic components enables manufacturers like Schneider Electric to build smaller, lighter, faster, and more efficient electrical distribution and protection products. Throughout its Smart Factory in Plovdiv, Bulgaria, the smallest components often play a large role in determining the effectiveness and quality of more than four million products per month. Situated across 12 acres, the factory is a vital manufacturing hub in Europe, supplying seven distribution centers in over 28 countries with electrical distribution and protection products, such as circuit breakers, for both consumers and businesses.
Soldering Inspection Too Challenging for Traditional Machine Vision
Manufacturing miniaturized electrical components is not without its various challenges. For example, soldering requires precision and can be an extremely complicated process. The process becomes even more complex when you consider the multiple conditions―from temperature to the placement of components―that can affect the final quality of a solder joint in an electronics device.
Ultimately, solder defects, such as cracks, voids, or weak bond strength, can impact the performance of a product, which can result in customer dissatisfaction. Manufacturers inspect, measure, and evaluate solder joints to identify defects. Traditional soldering inspection systems use high-resolution machine vision systems to scan various electronics components and their connection points, enabling manufacturers to examine the solder joints and surrounding areas to ensure quality.
However, the Schneider Electric Plovdiv manufacturing team found using conventional machine vision to perform soldering joint inspection was very challenging due to the high levels of variation in defect types, size, and location. Specifically they wrestled with the following:
• Inconsistent product quality
• Inefficient use of raw materials
• Inability to leverage inspection results data for process optimization
Schneider Electric Collaborates with Cognex Through Their Exchange Partner Ecosystem
When the time came to find a solution to improve the soldering inspection process, they turned to their own ecosystem of partners, Schneider Electric (SE) Exchange. Corporate partner communities, such as SE Exchange, help facilitate the types of partnerships that can tackle industry issues through co-innovation. Together, collaborative partners devise joint solutions that solve tough business challenges. Additionally, users of SE Exchange can leverage IoT solutions from companies like Cognex, that are compatible with the EcoStruxure™ architecture for their plant automation and energy management projects. From SE Exchange, we communicate with our partners in a very reliable and effective way. We share ideas and best practices in our area,” says Martin Yornadov, Method and Maintenance Manager at the Plovdiv plant. ”We decided to work with Cognex because they are a well-known partner of ours,” he adds.
Cognex has supplied machine vision and traceability systems to Schneider Electric plants worldwide for over 20 years. Over the past five years, Cognex has elevated its relationship with Schneider Electric by becoming a Schneider Electric Technology Partners Program (TPP) partner and promoting its products on the Exchange marketplace.
AI-Based Automated Soldering Inspection Delivers Many Tangible Benefits
A primary challenge at the Plovdiv factory revolved around automation. “It was important that, together with Schneider Electric applications and Cognex technology, we created a centralized solution that helped improve production efficiency in the Plovdiv factory,” says Yordanov. “Cognex skillfully developed solutions applicable to our EcoStruxure applications.”
Cognex vision systems support a large variety of protocols, which enables them to communicate with any type of PLC or external system. “With Cognex, we co-developed a few solutions in our process, which helped us produce better quality products,” says Yordanov. “As an example, we used Cognex’s In-Sight D900 with integrated AI-based technology which helped the plant improve the management of the soldering process.”
AI-based solutions embedded in the D900 vision system use neural networks to learn by example. The neural network is trained by providing some images or examples of what is a good part and what is a bad part. And based on that experience, the system can automatically separate good parts from bad parts.
With the development of Cognex AI-enabled inspection solutions, the applications at the plant not only are much easier to solve, but they also deliver very accurate results. This solution helps Schneider Electric deliver quality products to their customers on time. The Cognex In-Sight D900 combined with the DataMan barcode reading system enabled Schneider Electric to maximize the effectiveness of their inspection process.
Yordanov explains that with EcoStruxure, the plant can effectively track the process, and the Cognex solution helps them improve product quality. “The ultimate winner, in the end, is the client because they will receive quality products on time,” says Yordanov.
By improving visibility into production lines and automating the inspection process, the Plovdiv factory achieved the following benefits:
• Saved €40,000 per year
• Reduced Scrap on production lines
• Improved line productivity
• Less than 2 year Return on Investment (ROI)
A Bright Future Based on Trusted Partnership
The use of the Cognex solutions at the Plovdiv factory and numerous other Schneider Electric factories worldwide demonstrates the high level of trust between the two companies.
As for where this partnership is headed, the Cognex Global Account team sees two paths: leveraging application successes across Schneider’s manufacturing sites and co-development. The first one is with Schneider’s factories, to deepen the global partnership between the companies that was started years ago. By globally working with Cognex across their various manufacturing plants to adopt Cognex AI-based technology to drive inspections and image-based barcode readers for traceability solutions, Schneider increases the scale of improved production efficiency and increased product quality.
The second path speaks to Cognex and Schneider Electric jointly developing solutions that can be leveraged by mutual customers of both companies. Since Cognex has expertise in machine vision and AI-based technology and Schneider Electric has expertise in data analytics from industrial processes, like with the EcoStruxure Machine Advisor solution, there is great potential for collaboration which will provide added value to their mutual customers.
Cognex has several of its solutions listed on SE Exchange and will soon add others, including the In-Sight 2800 vision system which was launched in 2022. The In-Sight 2800 embeds edge learning technology. It is AI-based, easy to use and simple to deploy. Another benefit of this solution is that it doesn’t require any specific skill to set up, providing the power of edge learning to any user.
Source: https://www.cognex.com/en-my/blogs/machine-vision/schneider-electric-smart-factory-boosts-product-quality-using-ai-based-automated-inspection