Pneumatics vs. Hydraulics: Choosing the Right Power for Your Application
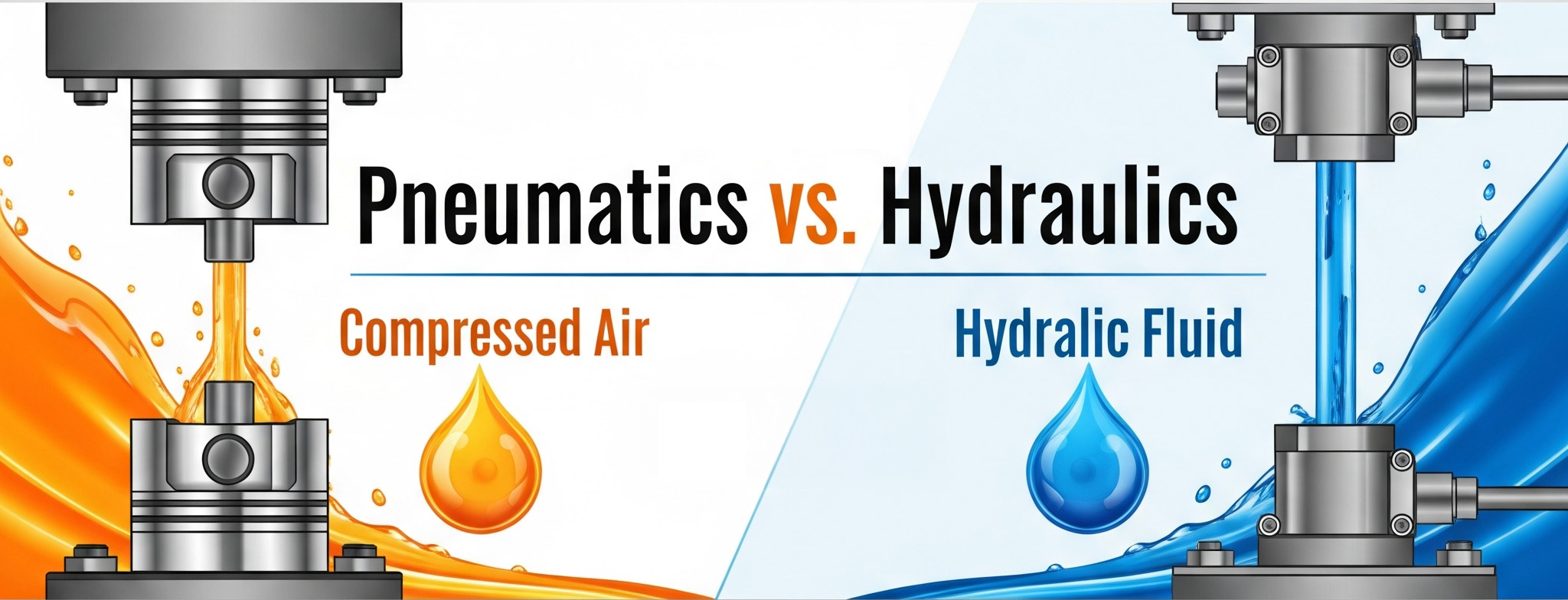
In the world of industrial automation, two powerhouses often go head-to-head when it comes to moving, lifting, and controlling machinery: pneumatics and hydraulics. Both are essential for various applications, but choosing the right one for your specific needs can feel like a dilemma.
Let’s break down the core differences between pneumatics and hydraulics to help you make an informed decision.
What’s the Basic Idea?
Both pneumatics and hydraulics are methods of transmitting power using fluids. The key difference lies in the type of fluid they use:
- Pneumatics: Uses compressed air or other gases. Think of it like a bicycle pump creating pressure to inflate a tire, but on an industrial scale.
- Hydraulics: Uses incompressible liquid, typically oil. Imagine squeezing a toothpaste tube – the force is directly transferred through the paste to push it out.
Pneumatics: The Agile Air Power
Pneumatic systems are known for their speed, simplicity, and cleanliness.
Pros of Pneumatics:
- Cleanliness: Since air is the working fluid, leaks aren’t messy and don’t pose environmental hazards. This makes pneumatics ideal for industries like food and beverage, pharmaceuticals, and cleanroom environments.
- Speed: Air can move very quickly, allowing for rapid movement of components and high-speed operations.
- Simplicity & Cost-Effectiveness: Pneumatic systems generally have simpler components and are often less expensive to install and maintain than hydraulic systems.
- Safety: Air is non-flammable, reducing fire hazards. Overloads often result in the system stalling rather than component damage, enhancing safety.
- Availability: Air is an unlimited and free resource.
- Tolerance to Temperature Changes: Less sensitive to temperature fluctuations compared to hydraulic oil.
Cons of Pneumatics:
- Lower Force Output: Compressed air provides less power than hydraulic fluid, making it unsuitable for very heavy-duty applications.
- Compressibility: Air is compressible, which can lead to less precise control and “spongy” movements if not properly managed.
- Noise: Air escaping can be noisy, though modern systems incorporate mufflers to reduce this.
- Air Quality: Requires filtration and drying to prevent moisture and contaminants from damaging components.
Ideal Applications for Pneumatics: Packaging, assembly lines, robotics (lighter applications), medical equipment, general automation, pick-and-place operations.
Hydraulics: The Heavy-Duty Workhorse
Hydraulic systems are the muscle of industrial machinery, capable of generating immense force.
Pros of Hydraulics:
- High Force Output: Liquid is virtually incompressible, allowing hydraulic systems to transmit tremendous power and lift incredibly heavy loads with compact components.
- Precision Control: Due to the incompressibility of oil, hydraulic systems offer very precise and rigid control over movement, making them excellent for applications requiring exact positioning.
- Self-Lubricating: The hydraulic oil provides constant lubrication to the system’s components, extending their lifespan.
- Constant Force/Torque: Can maintain constant force or torque regardless of speed changes.
Cons of Hydraulics:
- Messy Leaks: Oil leaks can be messy, hazardous, and require significant cleanup.
- Higher Cost & Maintenance: Hydraulic components are often more complex and expensive, and the systems require more specialized maintenance.
- Fire Hazard: Hydraulic oil can be flammable, posing a fire risk in certain environments (though fire-resistant fluids are available).
- Temperature Sensitivity: Oil viscosity changes with temperature, which can affect system performance. Requires cooling in high-power applications.
- Noise: Hydraulic pumps can be noisy.
Ideal Applications for Hydraulics: Construction equipment (excavators, bulldozers), heavy presses, injection molding machines, forklifts, aerospace applications, large-scale lifting operations.
Choosing the Right Power: A Quick Guide
To decide between pneumatics and hydraulics, ask yourself these questions:
- How much force do you need? For high force or heavy lifting, hydraulics is likely your answer. For lighter loads and quick movements, pneumatics shines.
- How precise does the movement need to be? If exact positioning and rigid control are crucial, hydraulics is usually better.
- What are your environmental concerns? If cleanliness is paramount (e.g., food processing), pneumatics is the clear winner. If minor oil leaks are acceptable, hydraulics might be fine.
- What’s your budget for initial setup and ongoing maintenance? Pneumatics generally offers a lower entry cost and simpler upkeep.
- What are the speed requirements? Pneumatics offers faster cycling for lighter tasks.
Both pneumatics and hydraulics play vital roles in modern industry. Understanding their strengths and weaknesses allows you to select the optimal power source for your specific application, leading to more efficient, reliable, and cost-effective operations.
Still unsure which system is right for your project? Our friendly product specialists are here to help! Contact us today for personalized advice and expert guidance.