10 Critical Considerations for Selecting Industrial Valves
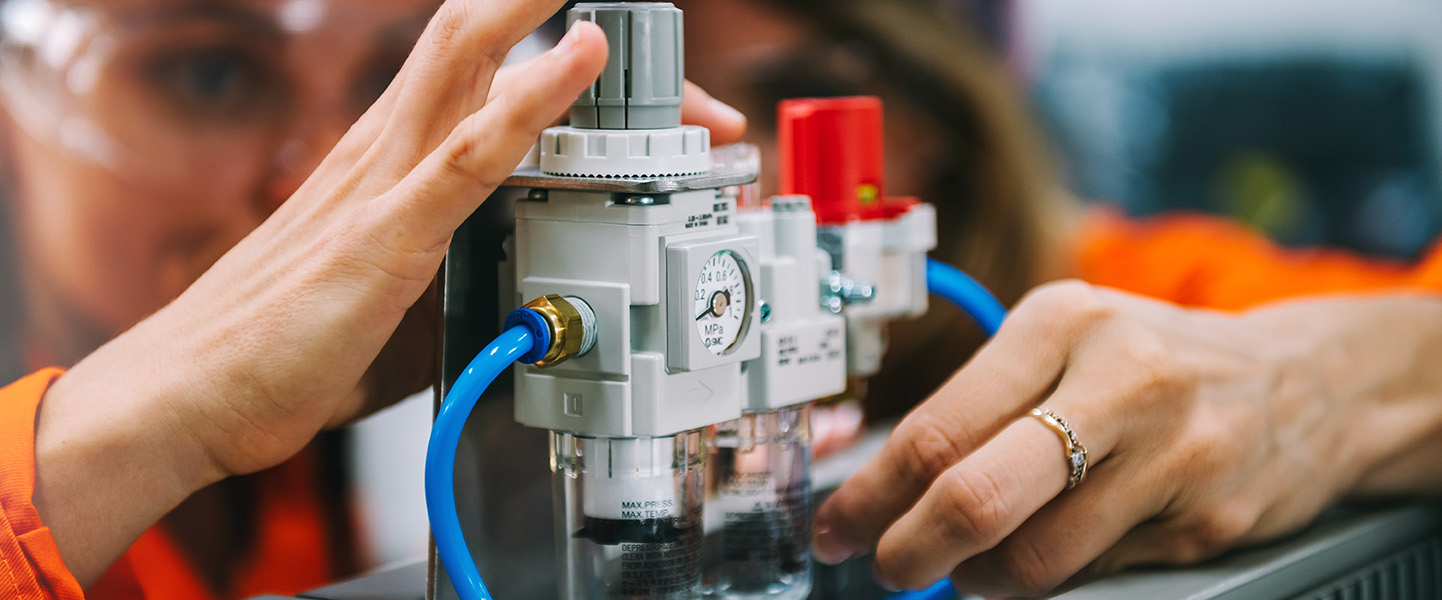
So, you’ve been assigned to choose industrial valves for your project or maintenance work. You’ve got a list of valves, sizes, and specifications – that’s a good start! But before you jump in, let’s delve into a comprehensive 10-step process to ensure your valve selection is grounded in thorough analysis rather than assumptions.
- Purpose of the Valve: Start by clearly defining the valve’s role in your system. Will it control flow, isolate media, or serve another function? Understanding its purpose is crucial for selecting the right valve type.
- Media Pressure: Ascertain the pressure of the media flowing through the valve. High-pressure applications require valves with robust construction and specialized sealing mechanisms to prevent leaks and ensure safety.
- Media Temperature: Consider the temperature range of the media. Valves exposed to extreme temperatures may require materials and designs tailored to withstand thermal stress and maintain sealing integrity.
- Type of Media: Analyze the characteristics of the media the valve will handle. Is it corrosive, abrasive, viscous, or reactive? Different media types demand specific valve materials and configurations for optimal performance and longevity.
- Environmental Conditions: Evaluate the environmental factors surrounding the valve’s installation location. Will it be exposed to harsh weather, corrosive chemicals, or abrasive particles? Select valves with coatings and materials suited to the environmental conditions to prevent premature degradation.
- Noise Level: Consider the noise level generated by the valve during operation. Noise reduction measures may be necessary, especially for valves near sensitive areas or where noise pollution is a concern.
- Manual vs. Automated Operation: Decide whether the valve will be manually operated or automated. Automated valves offer precise control and remote operation capabilities but require additional considerations such as actuation type and power sources.
- Control Requirements: Determine if the valve requires precise control over flow rates or positions. Control valves equipped with positioners or modulating actuators offer fine-tuned control over process variables, ideal for applications with stringent performance requirements.
- Valve Dimensions: Ensure the valve dimensions align with the available space for installation. Oversized valves may pose logistical challenges during installation and maintenance, while undersized valves can lead to flow restrictions and inefficiencies.
- Weight and Supports: Consider the weight of the valve and its impact on supporting structures. Large or actuated valves may exert significant loads on piping systems, requiring adequate support to prevent stress and structural damage.
By meticulously evaluating these ten critical considerations, you’ll confidently and precisely navigate the valve selection process. Don’t underestimate the importance of thorough analysis – selecting the suitable valves is essential for ensuring your industrial systems’ reliability, safety, and efficiency. Contact our product sales specialist to choose the best valves for your solutions.